Passionate People. Powerful Solutions.
Generator Repairs
When your diesel generator needs attention, Pleavin Power is here to help. With over 40 years of combined experience and engineers stationed across the UK, we provide expert repairs wherever and whenever you need them. Our commitment is simple – to get your generator running reliably as quickly as possible.
- 24/7 Nationwide Support
- Repairs on any generator model
- All spares in stock at Pleavin Power HQ
How Can We Help?
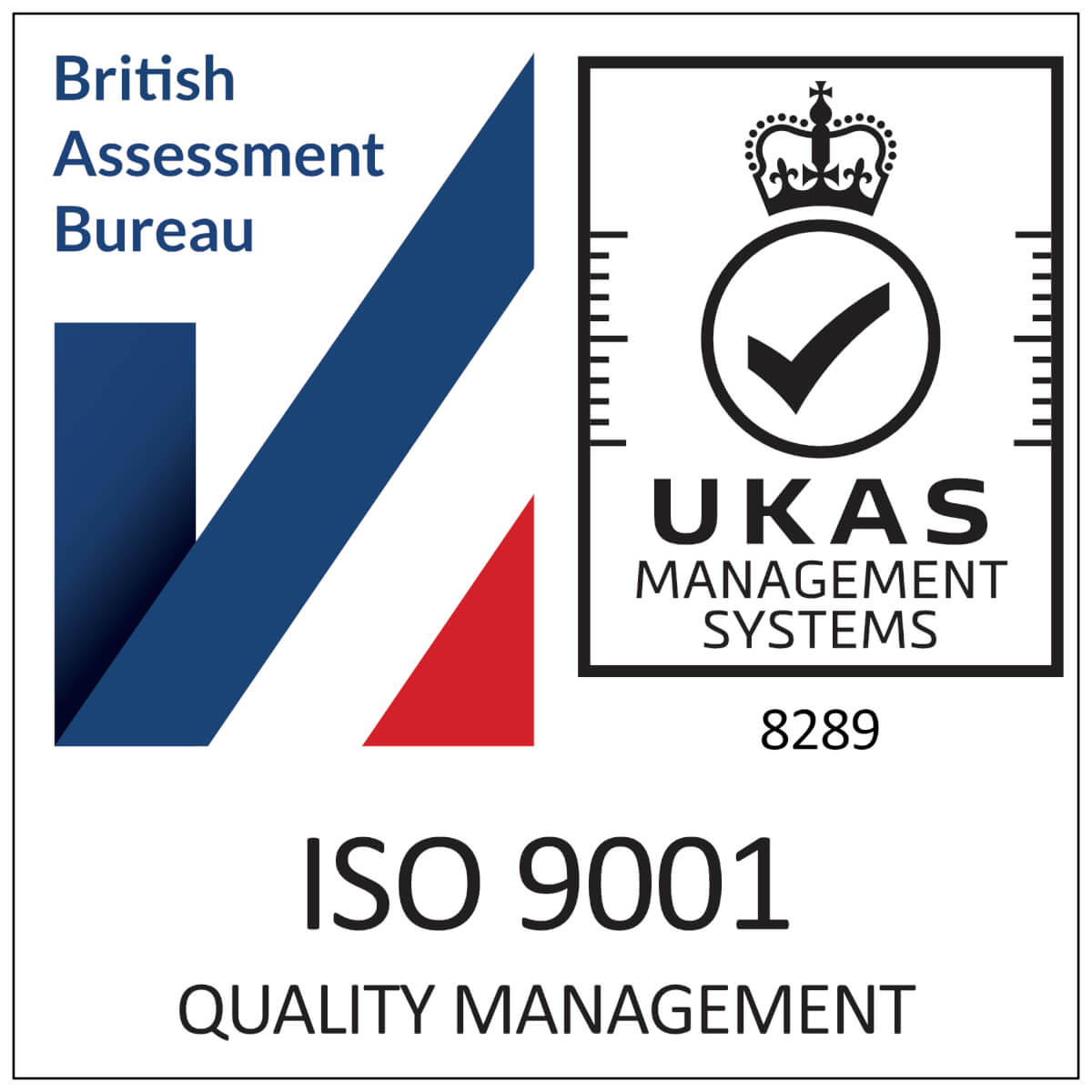
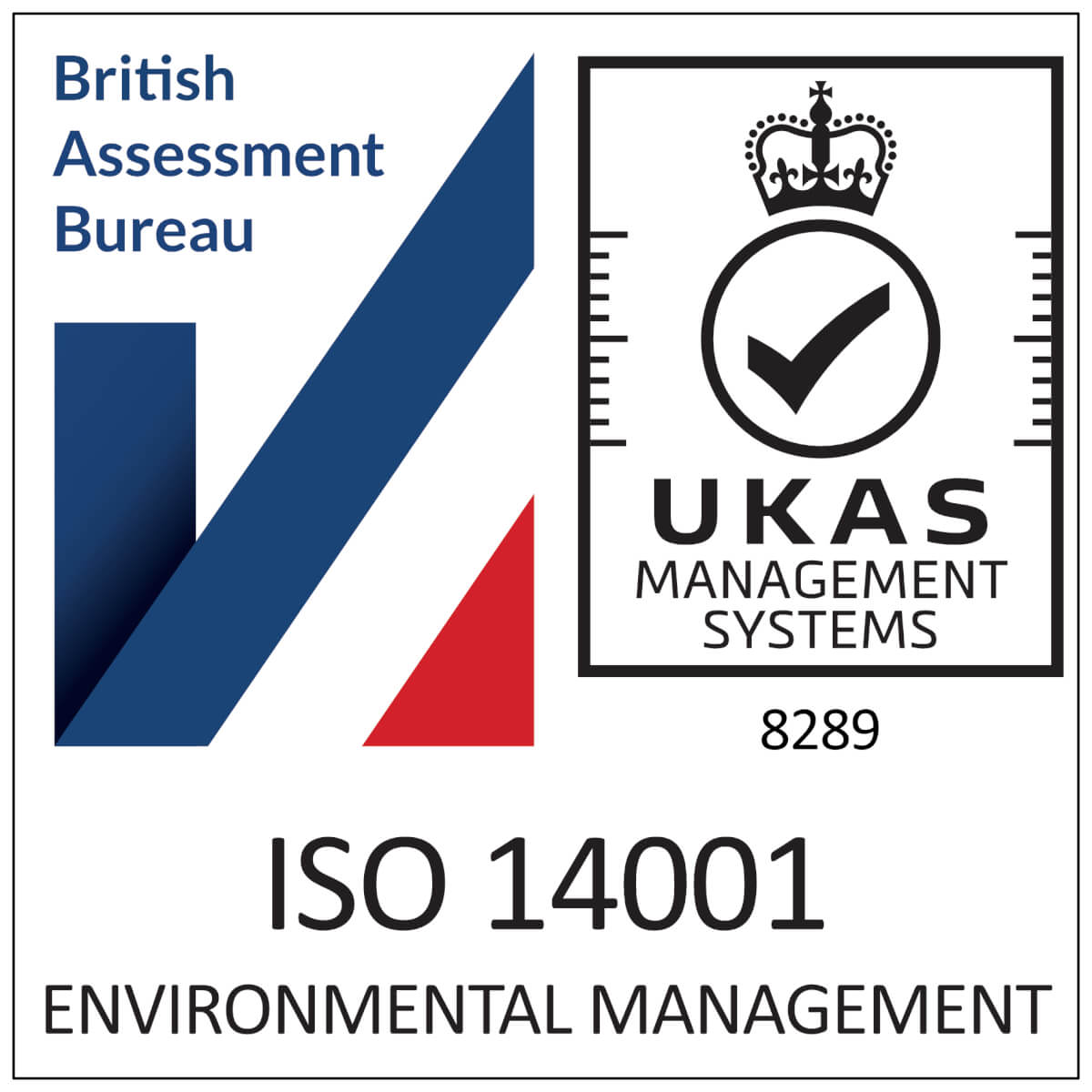
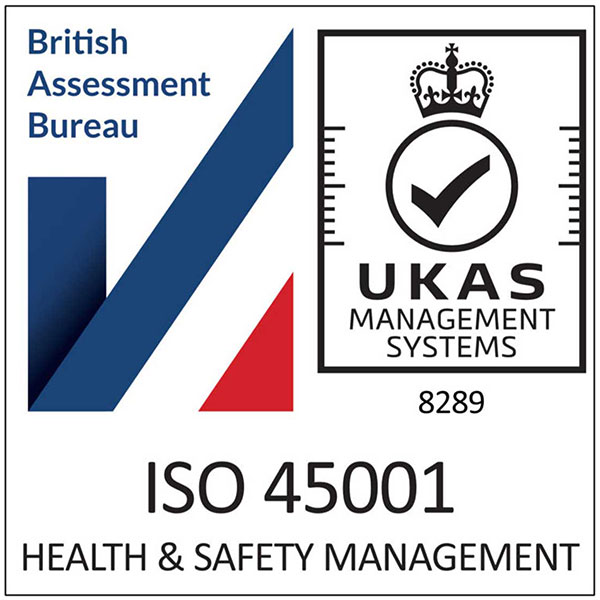
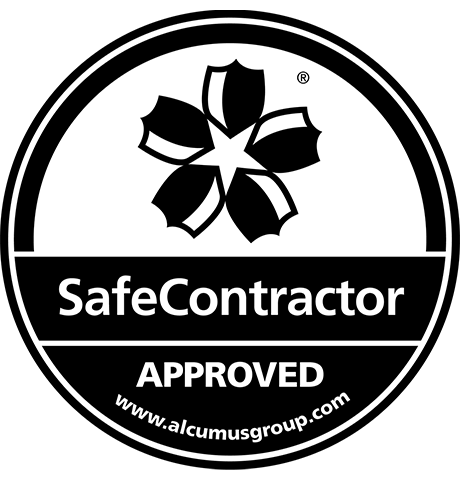
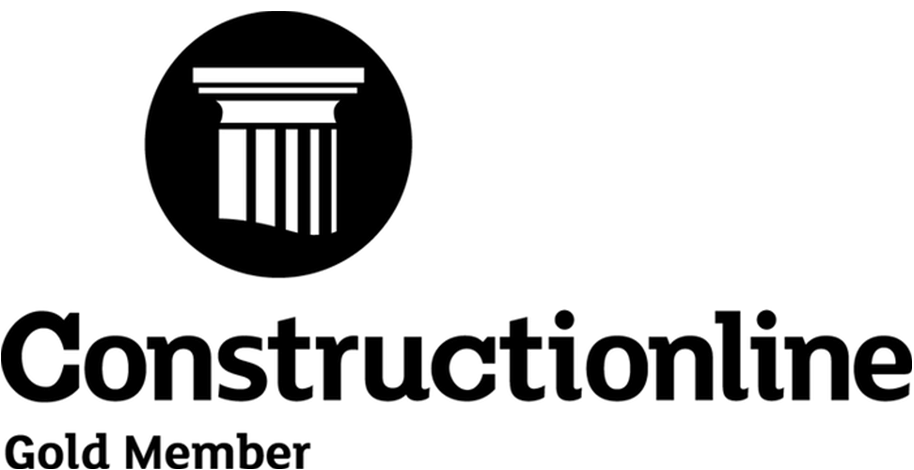
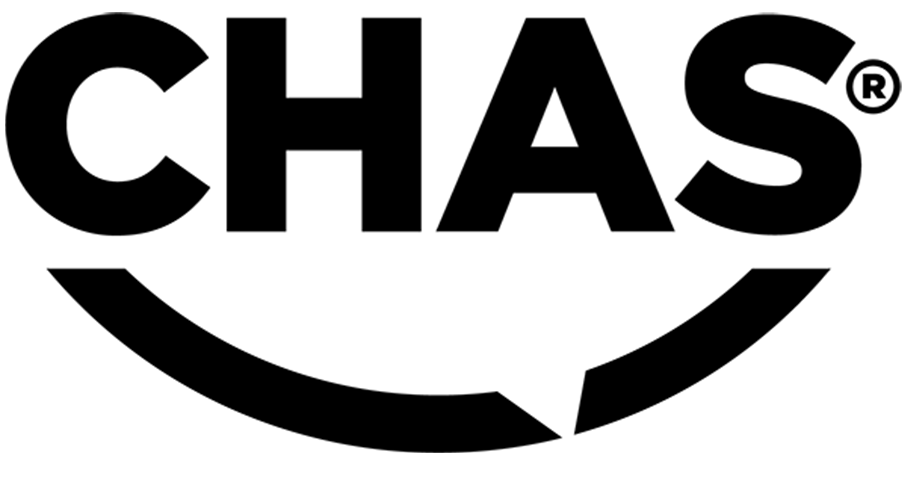
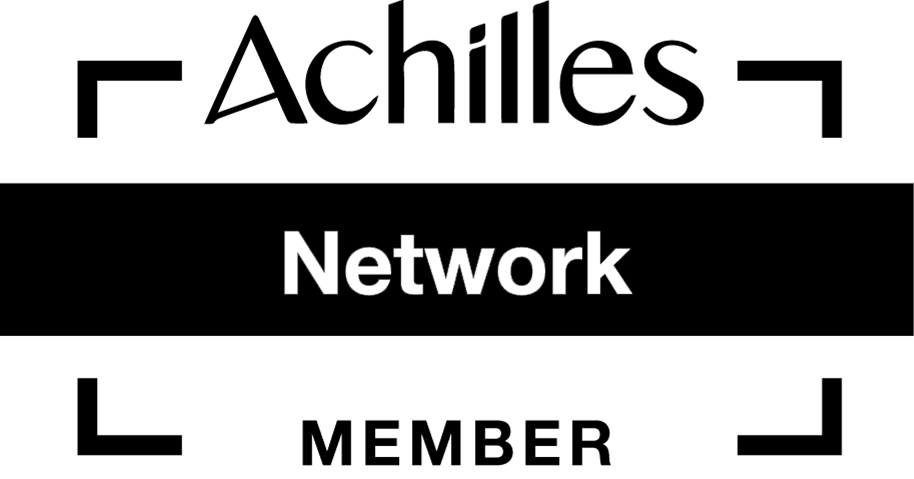
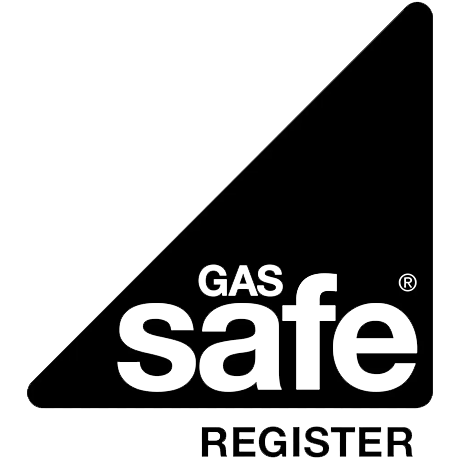
Why Are Repairs Needed?
Diesel generators are built tough, designed to deliver reliable power for years. However, like any machine, components wear out over time, and breakdowns become inevitable without regular care. Regular servicing can prevent most of these issues, ensuring your generator operates smoothly and reducing the need for frequent repairs.
Common issues include battery failures often caused by prolonged use or lack of maintenance and blocked fuel filters which can damage the generator and contaminate fuel. Overuse is another culprit as consistent heavy use accelerates wear and tear alongside a need for generator rewinding to help the winding coils inside return to their original output.
With engineers strategically located across the UK we can be on-site within 4 hours to diagnose and fix issues. Whether it’s a minor adjustment or a major repair we’ve got you covered.
Other Common Causes of Generator Failure
- Battery failure
- Low fluid Levels
- External fluid hoses failure
- Engine pre-heating failure
- Battery charger failure
- Automatic voltage regulator failure
- Catastrophic alternator winding failure
- Sensor malfunction or failure
- Controller malfunction or complete failure
Fixing Broken Down Generators
Repairs can vary in scale from fine tuning settings for better efficiency and output to full on part replacements, and everything in between. In the most critical of operations, such as hospitals, generators will operate in N+1 or N+2 configurations with UPS (Uninterruptible Power Supply) support. In this case when power failure or generator failure occurs, the UPS will support the load. Meanwhile the second generator starts up and takes over.
This gives time for important repairs, generator engine reconditioning and overhauls, and other services to be carried out.
Other operations may have different arrays or configurations and may require different fixes. No matter the issue our engineers arrive on site ready to diagnose it, equipped with the latest tools for the task and ready to work hard to get your generator back to how it should be.
Replace vs Repair
While we will always strive to repair a generator when it breaks there are times where it isn’t the best course of action. When it comes to maintaining reliable power the choice between repairing or replacing your diesel generator can be a tough decision. Both options have their advantages depending on the age, condition and requirements of your equipment:
Consideration
Repairing a Diesel Generator
Replacing a Diesel Generator
Cost
Lower upfront cost, making it a cost-effective solution for minor issues.
Costs more upfront but offers better long-term value with modern technology.
Downtime
Repairs usually have a quick turnaround, especially for minor faults.
Takes longer to install, but you get a fresh start with a brand-new setup.
Longevity
Extends the generator’s lifespan, making it a great option for well-maintained units.
Provides a fresh start with a new warranty and extended operational life.
Performance
Restores functionality in line with operational needs for older systems.
Delivers improved efficiency, reliability, and compliance with modern standards.
Environmental Impact
Keeps the generator in use, reducing waste from disposal or recycling.
New models are generally more environmentally friendly and efficient with fuel use.
Value
A great way to get more life out of your generator and stretch your budget.
A smart investment if the generator is nearing the end of its lifecycle or no longer meets operational needs.
Sectors
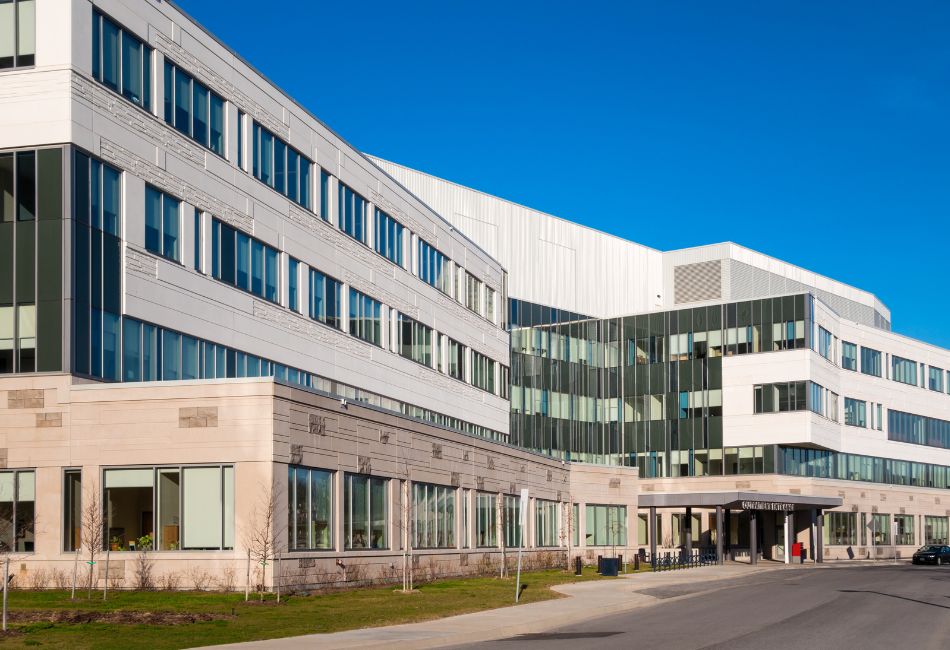
Public Sector
Whether routine repairs or a time-sensitive scenario, from schools to hospitals our engineers help keep essential services powered.
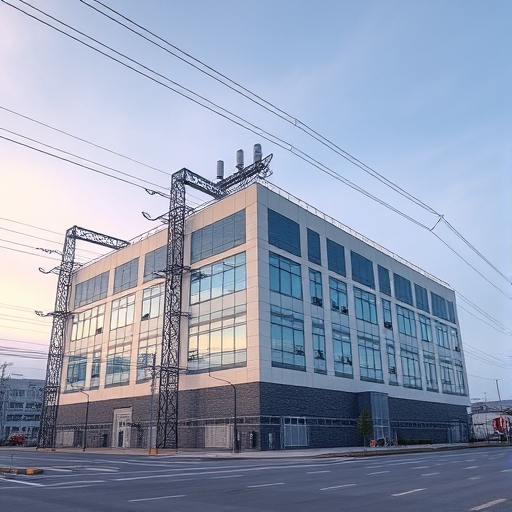
When your services require our repairs to keep running we won’t keep you waiting. Our goal is to keep power flowing, no matter the challenge.
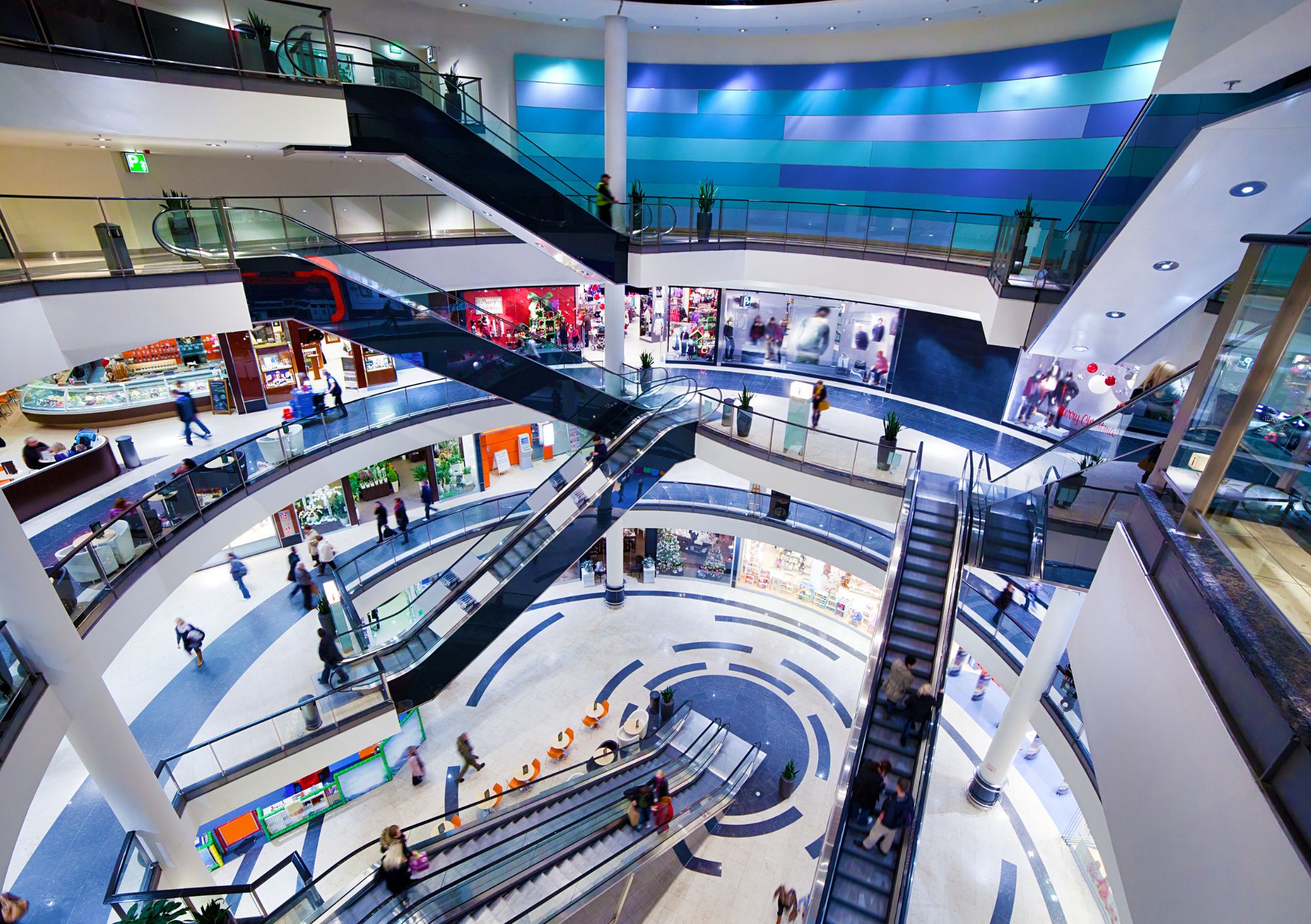
Keeping buildings powered means keeping generators running. Our diesel generator repairs tackle issues fast, keeping operations uninterrupted for managed facilities.
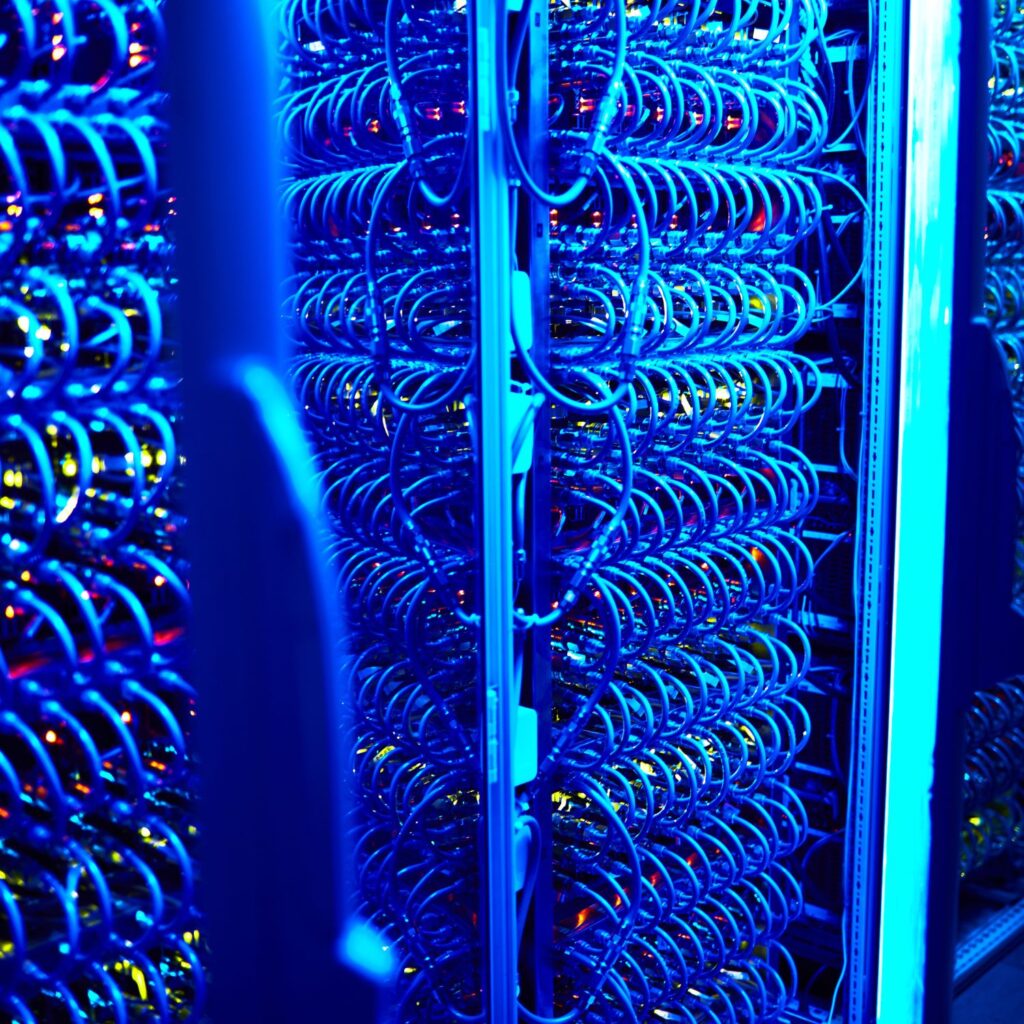
The data you hold needs flawless power to keep online, and we’re here to deliver. Blocked filters, automatic voltage regulator failures and other issues: We can handle it.
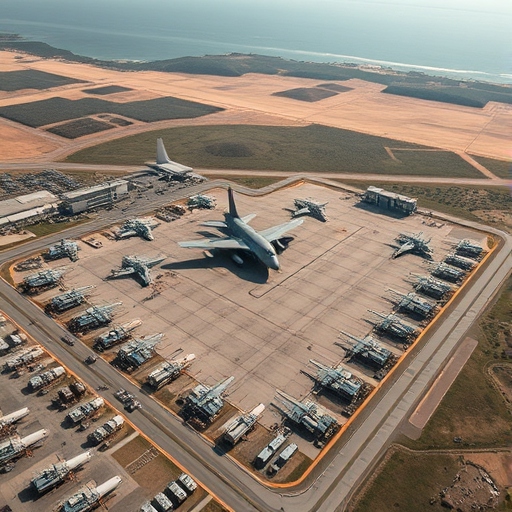
Land, sea, or air, your operations demand dependable power at all times. We provide rapid expert repairs to keep generators ready for deployment.
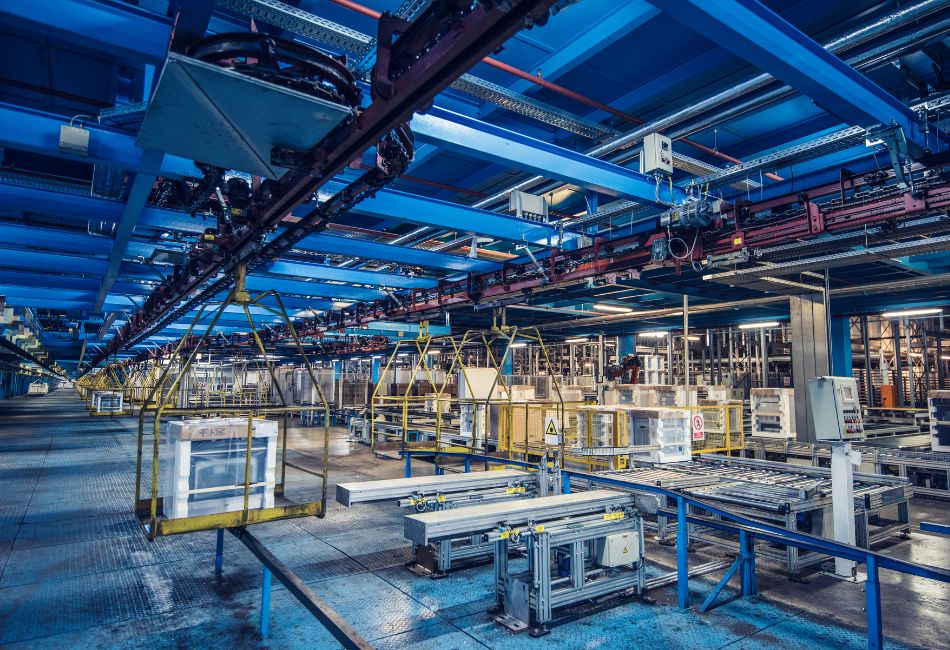
Manufacturing
Generators in industrial settings face heavy use but our repairs keep them running like clockwork. We’ll troubleshoot and fix the problem so production doesn’t miss a beat.
Case Studies
Animal Feed Manufacturer
When a global animal feed manufacturer was suffering downtime due to loss of electricity supply and their critical standby generator failed, Pleavin Power were called upon to support them.
Global Pharmaceutical Provider
When a global Pharmaceutical provider suffered generator issues Pleavin Power were recommended to the client and contacted to survey
Research Facility
Power loss affecting a research facility across five floors in central London posed significant challenges, potentially compromising ongoing experiments within the facility.
Global Shipping Organisation
Pleavin Power were contacted by the global shipping organisation after they had suffered from prime power failure whilst at sea